NEWS | SOFTWARE | SHEET
Alkali-Aggregate Reaction – Unveiling the Silent Threat to Concrete Durability
Alkali-aggregate reaction is a chemical process that occurs within concrete when certain aggregates react with the alkali content in the cement. This reaction leads to the formation of a gel-like substance, expanding over time and inducing internal pressure within the concrete structure.
The two primary types of AAR are alkali-silica reaction (ASR) and alkali-carbonate reaction (ACR), each involving specific types of aggregates.
Causes of Alkali-Aggregate Reaction:
- Aggregates Susceptible to AAR: Certain minerals within aggregates are prone to react with alkalis. In the case of ASR, reactive silica in aggregates, such as opal, chert, and strained quartz, triggers the reaction. For ACR, dolomitic limestone and certain dolomitic aggregates are the culprits.
- High Alkali Content in Cement: The alkali content in cement significantly influences AAR. High-alkali cements, often used for specific applications, can accelerate the reaction process, leading to quicker and more severe consequences.
- Moisture Content: AAR is influenced by the availability of moisture. Wet environments or structures exposed to water may experience more rapid and extensive AAR development.
Manifestations of Alkali-Aggregate Reaction
Visible Signs of AAR:
- Surface Cracking: One of the early signs of AAR is the development of map-like cracks on the surface of concrete. These cracks may be fine and exhibit a random pattern.
- Expansion and Disintegration: As the gel produced by the reaction expands, it exerts pressure on the surrounding concrete, leading to physical expansion and, eventually, the disintegration of the affected areas.
- Reduced Durability and Strength: Over time, the structural integrity of the concrete is compromised. The affected areas experience reduced durability and strength, making the structure susceptible to further damage.
Challenges in Detection
- Latent Period: AAR often has a latent period, during which there are no visible signs of distress. By the time symptoms become apparent, significant internal damage may have occurred.
- Non-uniform Manifestations: AAR may manifest differently in various parts of a structure, making it challenging to detect and assess uniformly. Some areas may exhibit severe damage, while others appear unaffected.
Preventive Measures and Mitigation Strategies
Aggregate Selection:
- Testing for Reactivity: Prioritize aggregates that are tested for reactivity. Various standardized tests, such as the ASTM C1293 for ASR, can determine the potential for aggregates to react with alkalis.
- Use of Low-Reactivity Aggregates: Opt for aggregates with low reactivity, reducing the likelihood of AAR. Proper screening and selection of aggregates can significantly contribute to preventing the occurrence of AAR.
Cement Selection:
- Low-Alkali Cements: Choose cements with low alkali content, especially in environments where reactivity is a concern. Low-alkali cements minimize the risk of AAR development.
- Blended Cements: Blended cements, such as fly ash or slag cement, can help mitigate the risk of AAR. These materials react with alkalis, reducing the overall alkali content in the concrete mixture.
Monitoring and Testing:
- Regular Structural Assessments: Implement routine structural assessments, including visual inspections and testing for potential AAR indicators. Early detection allows for proactive intervention.
- Advanced Testing Techniques: Utilize advanced testing techniques, such as petrography and scanning electron microscopy, to assess concrete microstructure and identify signs of AAR at a microscopic level.
Environmental Controls:
- Moisture Management: Implement measures to control moisture exposure, especially in structures susceptible to AAR. Proper drainage, waterproofing, and sealing can help minimize the impact of moisture on the reaction.
- Temperature and Humidity Control: Maintain optimal temperature and humidity levels during the curing process to mitigate the risk of AAR. This is particularly crucial in regions with varying climatic conditions.
Importance of Proactive Management
Economic Implications:
- Cost of Repairs and Rehabilitation: AAR-induced damage often necessitates costly repairs and rehabilitation efforts. Proactive management reduces the economic burden associated with extensive structural interventions.
- Avoiding Premature Structure Replacement: In severe cases, structures affected by AAR may face the prospect of premature replacement. Proactive measures can extend the service life of the structure, deferring the need for costly replacements.
Safety and Reliability:
- Structural Safety: AAR-induced damage compromises the safety of structures, posing risks to occupants and neighboring properties. Proactive management safeguards structural safety, ensuring the reliability of the built environment.
- Long-Term Structural Performance: Well-managed structures exhibit enhanced long-term performance, providing assurance to owners, developers, and users regarding the reliability and stability of the built environment.
To get more details, go through the following video tutorial.
Lecturer: Tyler Ley
Continuous Monitoring and Learning:
Implement a continuous monitoring and learning system to stay informed about the latest developments in AAR mitigation and prevention. Regularly update preventive measures based on advancements in research and technology to adapt to changing industry standards.
Education and Awareness:
Promote education and awareness within the construction industry about the risks and preventive measures related to AAR.
Foster a culture of proactive management by ensuring that architects, engineers, contractors, and other stakeholders are well-informed about the implications of AAR and the steps to mitigate its effects.
Collaborative Research Initiatives:
Encourage collaborative research initiatives between academia, industry professionals, and government bodies to further understand AAR mechanisms, develop innovative mitigation strategies, and establish updated guidelines for the construction industry. Sharing knowledge and insights can lead to more effective preventive measures.
Alkali-aggregate reaction may be a silent threat, but its potential impact on concrete structures is far from silent. Proactive management through careful aggregate and cement selection, regular monitoring, and environmental controls is paramount in mitigating the risks associated with AAR.
As the construction industry continues to evolve, understanding and addressing these nuanced challenges contribute not only to the longevity of structures but also to the safety and economic sustainability of the built environment. By adopting comprehensive preventive measures, remaining vigilant through advanced testing and monitoring, and embracing a culture of continuous learning, stakeholders can ensure that concrete structures stand the test of time in the face of the silent threat that is alkali-aggregate reaction.
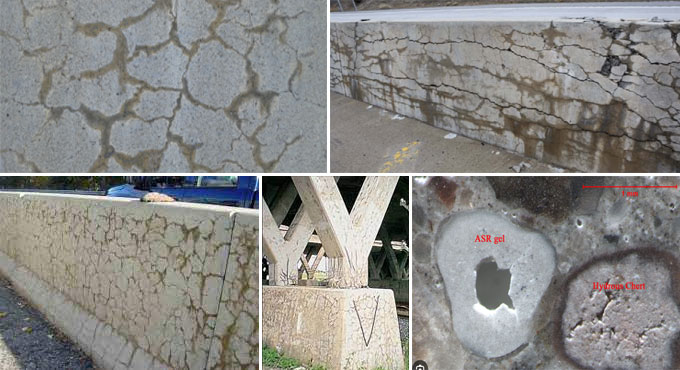