NEWS | SOFTWARE | SHEET
Exploring the Depths of Cast-In-Situ Concrete: Advantages, Disadvantages, and Casting Techniques
In the realm of construction, the choice of building materials and techniques plays a pivotal role in determining the durability, strength, and overall quality of a structure. One such method that has stood the test of time is cast-in-situ concrete, also known as cast-in-place concrete. This construction technique involves pouring concrete directly into the formwork at the construction site, where it is allowed to set and cure, forming a seamless and robust structure.
Understanding Cast-In-Situ Concrete
Cast-in-situ concrete is a construction method that involves pouring fresh concrete into a specific mould or formwork at the construction site.
Unlike precast concrete, which is cast and cured in a controlled environment before being transported to the construction site, cast-in-situ concrete is mixed and poured on-site. This method offers a high degree of flexibility, allowing for customization and adaptability to the unique requirements of each construction project.
Advantages of Cast-In-Situ Concrete
Customization and Adaptability
One of the primary advantages of cast-in-situ concrete is its ability to be customized according to the specific needs of a project. The flexibility in adjusting the mix of design, formwork, and casting techniques enables architects and engineers to create unique and intricate structures.
Seamless Integration
Cast-in-situ concrete provides a seamless integration of structural elements, eliminating joints that may weaken the overall integrity of the structure. This continuity enhances the load-bearing capacity and reduces the risk of structural failure.
Cost-Effective
In many cases, cast-in-situ concrete proves to be more cost-effective than precast alternatives. The elimination of transportation costs for precast elements and the efficient use of materials on-site contribute to overall cost savings.
Strength and Durability
The curing process of cast-in-situ concrete takes place in its final position, allowing for a more robust and durable structure. This method ensures that the concrete achieves its maximum strength potential, contributing to the longevity of the construction.
Versatility in Design
Cast-in-situ concrete allows for greater versatility in architectural design. It can be moulded into various shapes and sizes, making it suitable for a wide range of applications, from simple slabs and columns to complex geometries.
Disadvantages of Cast-In-Situ Concrete
Curing Time
One notable disadvantage of cast-in-situ concrete is the extended curing time required on-site. The curing process is essential for achieving optimal strength, and in some cases, it may delay construction schedules, especially in projects with tight timelines.
Weather Dependency
The success of cast-in-situ concrete is often weather-dependent. Extreme temperatures, rainfall, or other adverse weather conditions can impact the curing process, potentially leading to issues such as cracking or reduced strength.
Labor-Intensive
The on-site nature of cast-in-situ concrete makes it labour-intensive. Skilled labour is required for the proper mixing, pouring, and finishing of the concrete. Additionally, the need for formwork installation and removal adds to the overall labour costs.
Formwork Complexity
Achieving intricate designs with cast-in-situ concrete may require complex formwork, which can be time-consuming to set up and dismantle. This complexity can also contribute to increased costs and potential difficulties in achieving consistent finishes.
Limited Quality Control
Unlike precast concrete, which undergoes quality control in a controlled environment, cast-in-situ concrete is subject to on-site variations. This can lead to inconsistencies in the mix, curing conditions, and overall quality, potentially affecting the structural integrity.
Casting Techniques for Cast-In-Situ Concrete
Slip Formwork
Slip formwork is a continuous casting method that involves the gradual upward movement of a formwork system as the concrete is poured. This technique is commonly used for constructing vertical structures like towers and chimneys. The continuous motion ensures a smooth and even finish, and the method is known for its efficiency in high-rise construction.
Jump Formwork
Jump formwork is another vertical casting technique used in the construction of tall structures. Unlike slip formwork, jump formwork is lifted vertically in discrete sections, allowing for greater flexibility and control. This method is suitable for structures with repetitive floor plans, such as residential or commercial towers.
Tunnel Formwork
Tunnel formwork is a casting technique that involves the use of a reusable formwork system, typically in the shape of a tunnel. The formwork is moved horizontally from one location to the next, and as it progresses, concrete is poured into the formwork, creating walls and slabs simultaneously. This technique is popular for constructing repetitive structures like residential buildings.
Flat Slab Casting
Flat slab casting is a common technique for constructing horizontal slabs without beams. In this method, the concrete is poured into the formwork, and after curing, a flat and smooth slab is achieved. This technique is often used in buildings where a clean and open floor plan is desired.
To get more details, go through the following video tutorial.
Lecturer: Civil Engineering
Prestressed Concrete Casting
Prestressed concrete casting involves preloading the concrete with tension before subjecting it to compressive loads. This technique enhances the structural efficiency of the concrete by counteracting tensile forces. It is commonly used in the construction of bridges, parking structures, and other applications where long spans are required.
Tilt-Up Construction
Tilt-up construction involves casting concrete panels horizontally on the ground and then tilting them into a vertical position using cranes. This technique is popular for the construction of warehouses, industrial buildings, and other structures with large, repetitive wall sections.
In conclusion, while the advantages of cast-in-situ concrete are numerous, success hinges on a holistic approach that considers the interplay of project planning, quality control, workforce competence, and ongoing maintenance.
By addressing these considerations, construction professionals can harness the full potential of cast-in-situ concrete, creating structures that stand the test of time while meeting the evolving demands of the built environment.
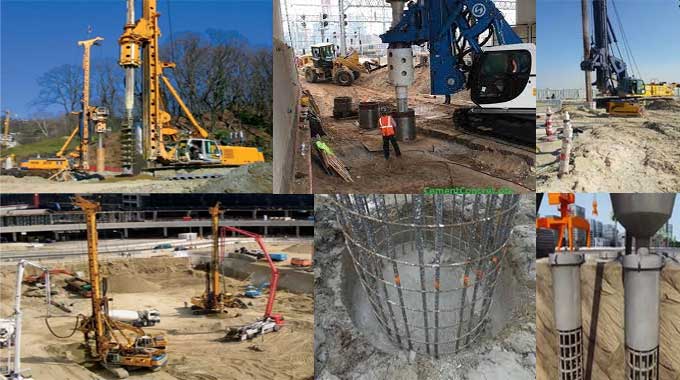