NEWS | SOFTWARE | SHEET
Putting Chenab arch bridge on the map as world's highest rail bridge
The majestic arches of the iconic Chenab Arch Bridge were completed, reaching a height of 359 meters above the riverbed and 30 meters higher than the Eiffel Tower in Paris. The Chenab Rail Bridge connects Bakkal and Kauri in Reasi district, Jammu and Kashmir, about 42 km from the main town of Reasi.
Features of Chenab Arch Bridge
A bridge built from this material will withstand earthquakes of magnitude eight and high intensity blasts. Temperatures below 20 degrees Celsius and winds over 200 kilometers per hour will also be metal resistance.
There will be a 14 meter dual carriageway and a 1.2 meter wide central verge on the bridge, which is designed for a speed of around 100 km per hour and a lifespan of 120 years.
This bridge will provide all weather connectivity between Kashmir and the rest of the country. It has already been connected at the bottom of the main arch, and now the upper arch needs to be completed to close the arch. Next, tracks will be laid on this new bridge.
Site Geology
With faults, folds, shear zones, & much more, the Himalayas offer geological surprises. The region is currently experiencing tectonic activity. Before building any major structure in the Himalayas, it is important to study the geology of the area.
- Tunnels and bridges will be constructed in difficult Himalayan geology on this mountainous railway line. A major challenge of the project is crossing the Chenab River.
- In addition to the Shiwaliks, there are pre-tertiary rocks on the site. Among the main subtypes of rocks are dolomite and limestone. Rocks such as quartzite and shale are found at some of the pier locations.
- Both abutments do not have significant shear zones or cavities. Abutment rocks display a blocky mass of highly fractured top layers. Rocks at the bottom are stable & strong enough to serve as a good foundation.
- Foliation joints are located on both abutments, with two sub-vertical joints per abutment.
- There is an extremely small distance between the foliation joints. No or little infill is present in the joints, making them irregular and rough. There is a high degree of interlocking in the dry rock mass.
Slope Design & Foundation
- There is a long distance between the base of the foundation and the groundwater table.
- There may be some hydrostatic pressure developed by rainwater over a short period of time. As a result, hydrostatic pressure was taken into consideration in the foundation analysis.
- The foundation analysis considered a higher seismic load factor, in addition to the usual load combination, because the bridge is located in a higher seismic zone.
- For geological logging and plate load testing of the foundations from 2 to 3 meter deep, trial pits were excavated.
- On both sides of the abutments, isolated footings and concrete pedestals were constructed. Each concrete pedestal of each foundation was supported by steel piers bolted to a base plate.
- Foundation construction of the 18 piers was carried out using structural steel piers.
- Both left and right abutments were analyzed for wedge failure. Based on a preliminary structural analysis both left and right abutments failed at the downstream side.
- The amount of anchor bolts and the degree of stabilization required were determined by a detailed analysis of wedge failure.
Construction Methods
Despite the lack of proper transportation to the bridge site, structural steel parts were manufactured in nearby workshops. On both sides of the valley, workshops and paint shops were constructed.
To get more details, watch the following video tutorial.
Lecturer: NEWS STATION
The site was without electricity and the water available in nearby channels wasn't suitable for concrete production. In order to supply river water from faraway mountains, electricity and water were produced on site.
- The first step was to begin work on the foundation and slope stabilization. The project involved the construction of 18 piers.
- The main span of the bridge will be erected using a cable crane. Construction workers will retain the cable crane at the site to use for future repair and maintenance projects.
- Workshop personnel will fabricate the bridge deck panels. Since the welding points are located under the bridge, the size of the panels is limited to 8 m.
- Steel structures weigh 25,000 tons on the bridge. Construction of solid steel columns of 100 m length will be carried out with the assistance of a cable crane that can handle 34 tons of weight.
Project Cost & Competition
This bridge is part of a 272 km rail link project being built by Northern Railway of India, which has been cited in various rail budgets of the country around 28,000 crore.
Steel was specifically chosen for the bridge's construction to reduce the project's cost.
Contractual issues delayed the bridge's completion in 2018 despite its scheduled completion by the end of 2019. The project's construction was also delayed due to the Coronavirus pandemic. The revised timeline for completion is December 2022.
Initial plans called for connecting Kashmir's northernmost city Baramulla to New Delhi via a rail link which was prepared in 2002. The Bharatiya Janata Party Atal Bihari Vajpayee government gave high priority to the project, but weather conditions and contracts delayed it.
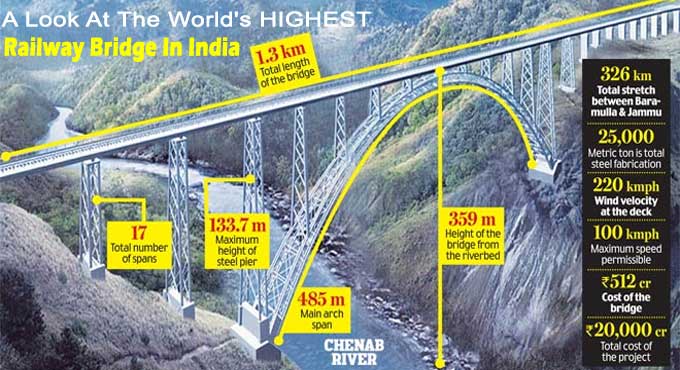