NEWS | SOFTWARE | SHEET
Aspects of Roller Compacted Concrete along with Merits & Demerits
In its unhardened state, roller compacted concrete slumps stiffer than conventional concrete. As a result, it can withstand the vibration required for complete compaction.
Layers approximately 20 cm to 30 cm thick are placed on top of each other. Layering concrete allows the concrete to be fully compacted.
When the concrete has been fully compacted, it achieves all of the desired properties, including destiny, strength, and texture. Concrete compacted with rollers is economical, as it does not need to be finished and can be used without formwork.
Define Roller Compacted Concrete
Concrete may not have the same proportion of ingredients as conventional concrete.
The same ingredients are used in roller compacted concrete as in traditional concrete. As a partial replacement for Portland cement, fly ash is added along with the common ingredients.
The raw materials or ingredients that are used in roller compacted concrete are the same as those used in conventional concrete. To give concrete special properties, chemical admixtures have been used such as water reducers, retarders, accelerators, and super-plasticizers.
Concrete produced in this way has a different proportion from conventional concrete. To replace Portland cement with fine aggregate and coarse aggregate, fine aggregate, coarse aggregate, and water fly ash are also added. Compared with traditional concrete, roller compacted concrete contains more chemical admixtures.
Roller Compacted Concrete Properties
Flexural Strength
Concrete roller compacted at 500 psi to 1000 psi has good flexural strength. There is a direct relationship between the flexural strength of this concrete and its density and compressive strength.
Shrinkage
Compared to conventional concrete, this concrete typically shrinks less and cracks less because of its lower water content.
Compressive Strength
In comparison with conventional concrete, roller compacted concrete has a compressive strength of 4000 psi to 6000 psi. The compressive strength of some structures has also exceeded 7000 psi. The reason for this is the low water cement ratio. Concrete achieves high compressive strength due to its low water cement ratio.
Bond Strength
Concrete is poured in layers after it has been roller compacted. The layer of material is placed and compacted to a thickness of 20 cm to 10 cm. After that, the next layers are applied following the same procedure. These layers must be tightly bonded together for the foundation structure. Sufficient bond strength cannot be achieved unless the concrete layers are thoroughly bonded.
Roller Compacted Concrete Merits
The mixture has a low water content, which makes it strong and durable. It is not necessary to use reinforcement bars when constructing a concrete element using this type of concrete.
When heavy loads are applied to it, it does not deform. Contrary to conventional concrete, it is a more cost effective option. Roller compacted concrete gives a smooth surface finish are resistant to oil spills, fuels, hydraulic fluids, and other such liquids.
Because fly ash is used as a partial replacement for cement in roller compacted concrete, cement consumption is reduced. Despite its high temperature resistance, it is durable.
Roller Compacted Concrete Demerits
Despite the efficiency of these dams when compared to other low cost options, they can be more costly in some instances. When the dams are not compacted properly, leakage may occur.
To get more details, go through the following video tutorial.
Lecturer: Gallagher Group
Roller Compacted Concrete Uses
The use of concrete pavement on roads, streets, and highways is also widespread. A variety of concrete dams, port and airport facilities, storage facilities, and parking lots may be constructed and rehabilitated. Light & heavy duty industries use roller compacted concrete facilities for construction and maintenance.
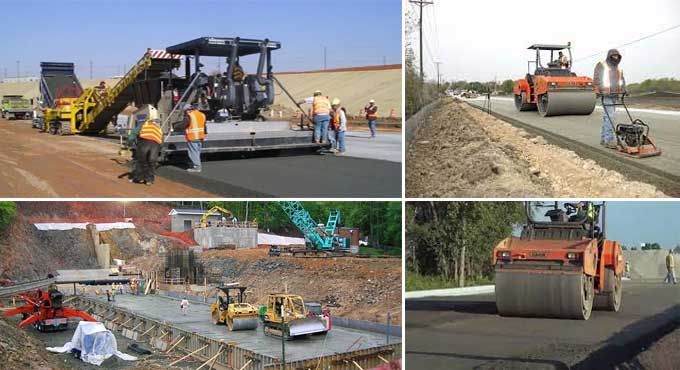